When dealing with tasks that involve lifting or rigging, understanding the difference between working load limit (WLL) and breaking strength is crucial for ensuring safety and efficiency. The working load limit is the maximum safe force that can be applied to equipment under normal conditions. It acts as the guiding metric for determining how much weight or stress a piece of equipment can handle regularly without risk of failure.
Breaking strength, on the other hand, is the amount of stress or weight that a component can withstand before it fails or breaks. This measurement is determined under ideal conditions and is not meant for regular operational use. The working load limit is derived from the breaking strength and is a significantly reduced percentage to maintain safety margins and account for variables that might affect performance over time.
Key Takeaways
- WLL is the safe force that equipment can handle during regular use.
- Breaking strength is the maximum force equipment can withstand before failure.
- Knowing both values ensures the safe and efficient use of lifting and rigging gear.
Understanding Working Load Limit (WLL)
When handling any load-bearing activities, your safety is paramount. That’s why understanding the Working Load Limit (WLL) is critical—it keeps you and your equipment safe.
Definition and Importance of WLL
Working Load Limit (WLL) refers to the maximum load that you can safely apply to equipment without causing damage or failure. This limit is set by the manufacturer. The WLL is a fraction of the ultimate breaking strength—it includes a safety margin to ensure the stability and longevity of the equipment.
Why is WLL important for you to know? It’s simple:
- Ensures the safety of both the user and the materials being handled.
- It prevents overloading, which can lead to equipment failure.
- Helps in selecting the correct equipment for your load-bearing activities.
Calculating WLL
To determine the WLL, manufacturers use a safety factor. This is a ratio that varies depending on the type of equipment and its intended use. However, as a general rule, the safety factor is often around:
- 3:1 for lifting slings
- 4:1 for wire ropes
- 5:1 for chain
- 6:1 for fiber rope
Here’s a straightforward way to calculate the WLL:
- Obtain the breaking strength (sometimes called break strength), which is the amount of force the equipment can withstand before failing.
- Divide the breaking strength by the safety factor provided by the manufacturer.
For instance, if a chain has a breaking strength of 10,000 pounds and a safety factor of 5, the WLL would be:
10,000 lbs (Breaking Strength) / 5 (safety Factor) = 2,000 lbs WLL
It’s vital for you to adhere to the WLL to maintain operational safety and avoid compromising the integrity of your load-bearing equipment. Always check the WLL on the equipment’s identification tag or consult the manufacturer’s specifications before use.
Breaking Strength and Its Significance
In the world of materials and equipment, breaking strength is a crucial safety benchmark. Understanding what it means helps safeguard the use of various products and ensures their safe handling.
Defining Breaking Strength
Breaking strength, not to be confused with working load limit (WLL), is the maximum force that an item can withstand before it fails or breaks. It’s a measure of tensile strength—the max tension your equipment can take. Manufacturers determine this value through rigorous testing, providing a guideline for the ultimate strength of materials like ropes, straps, and chains.
- Breaking Strength: Maximum force absorbable without failure
- Tensile Strength: Reflects how strong the material itself is
This value is not what you should use to determine the everyday load your equipment handles. Instead, it’s a figure provided for understanding the absolute limits of the material, which is why your equipment’s manufacturer will set this value.
Determining Break Strength
Manufacturers put their products through a series of tests to establish break strength, ensuring that they comply with safety standards. This is fundamental for the safe adoption of the products as the outcomes of these tests dictate the maximum load they determine the product can safely take one time before it risks breaking.
You should always refer to the documented breaking strength given by your equipment’s manufacturer to know the force limit, but keep in mind that this is not a number you should be reaching during regular use.
The Relationship Between WLL and Breaking Strength
Before delving into the specifics, it’s important to understand that the Working Load Limit (WLL) and Breaking Strength are distinct measures, each serving to ensure your equipment is used within safe parameters.
Comparison and Contrast
Here’s a simple comparison table to help you visualize the relationship:
Aspect | Working Load Limit (WLL) | Breaking Strength |
---|---|---|
Purpose | Safety limit for regular use | Absolute maximum force capacity |
Set by | Manufacturer | Material properties/testing |
Reflects | Safety, usability, and life of equipment | Material capabilities |
Used for | Daily operations | Testing and certification |
Value | Less than Breaking Strength | Greater than WLL |
Real-life Application in Equipment Safety
In practical terms, you’ll see these measures deployed for equipment like lifting slings, chains, straps, and shackles. Safe Working Load was a term historically commonly used for WLL; however, WLL is more consistently applied across industries today.
The Factor of Safety is a ratio that denotes how much stronger the item is than its stated WLL. For example, if a chain has a WLL of 2,000 pounds and a Breaking Strength of 6,000 pounds, the Factor of Safety is 3. This factor acts as a buffer against unexpected loads, misuse, or wear over time..
Avoiding Common Mistakes
Confusion between WLL and BS: You might mistake WLL for the maximum tension the tie downs can handle. Actually, WLL is typically a third of the BS. It’s the maximum load that should be applied to the equipment during normal use.
- Exceeding WLL: Do not exceed the WLL; doing so can lead to failure. Always adhere to the manufacturer’s recommendations.
- Misinterpreting Shock Load: Any load that changes rapidly is a shock load, which can cause unexpected stress on your tensioning device and tie downs. When a shock load occurs, the force applied can be significantly greater than the static load, potentially causing failure even if the weight is within the WLL under normal conditions.
- Improper Use of End Fittings: The end fittings of tie downs have their own rated capacity. Ensure they are compatible with the WLL of the whole assembly.
Clarifying Terminology and Usage
Breaking Strength (BS): This is the point at which the product, whether it’s a tow strap or shackle, will fail under a load. It’s the maximum force a product can withstand before failure occurs. For instance:
Product | Breaking Strength | Working Load Limit |
---|---|---|
Tow Strap | 15,000 lbs | 5,000 lbs |
Shackle | 30,000 lbs | 10,000 lbs |
Remember, you should not use the product up to its breaking strength; you should operate within the WLL to maintain safety.
Italicize key terms the first time they are used to highlight their importance, such as WLL and breaking strength. This helps you to understand which terms are crucial and their definitions, making it less likely that you will confuse them. Always refer to the manufacturer’s guidelines for the proper WLL, and remember that these ratings are based on ideal conditions, and real-world scenarios like knotting or bending can reduce the working load limit significantly.
Safety Considerations and Best Practices
When handling materials and equipment, your safety hinges on respecting the Working Load Limit (WLL) and understanding how the Safety Factor determines its value. Regular inspections are vital to prevent failure and mitigate dangerous situations.
Maintaining a Safe Working Load
Your Role:
- Always adhere to the manufacturer-recommended WLL, which is the maximum load your equipment can handle under normal conditions.
- Avoid exceeding this limit as it can lead to equipment failure, endangering both you and the load.
Best Practices:
- Check labels and documentation for specific WLL before use.
- Plan lifts carefully to not surpass the WLL, thus ensuring a margin of safety.
Factors Influencing Safety Factor
Safety Factor Defined:
The Safety Factor is the ratio between the Breaking Strength (the point at which your equipment will fail under stress) and the WLL. Typically, the industry standard for the Safety Factor ranges from 5:1 to 12:1, depending on the type of equipment and its use case.
Critical Considerations:
- The more demanding the conditions, the higher the Safety Factor should be.
- Note that different equipment types (ropes, straps, etc.) may have varying Safety Factors.
Inspection Regimens:
- Conduct regular inspections of all lifting gear.
- Look for any signs of wear, damage, or corrosion that may affect the WLL or Safety Factor.
- Replace or repair any equipment that does not meet the necessary safety standards.
By maintaining a clear understanding of these factors and following these guidelines, you’re taking a significant step toward ensuring a safer working environment.
Materials and Construction
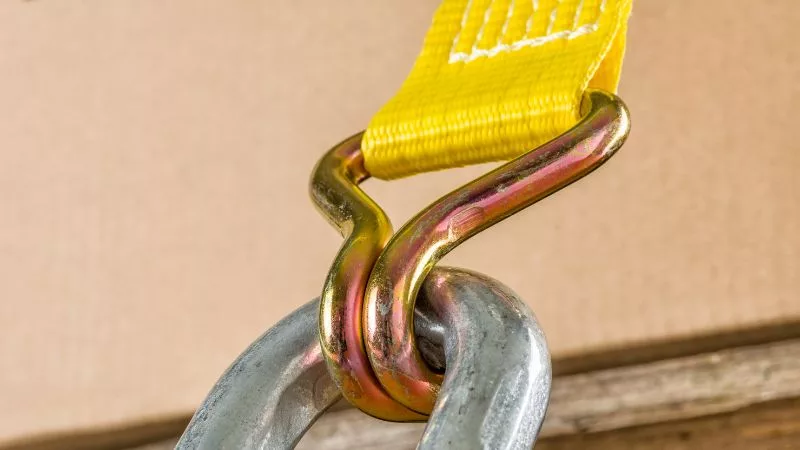
In the world of load management, the materials and construction of your equipment are pivotal. They determine both the Working Load Limit (WLL) and the breaking strength of your straps, ensuring you can transport goods safely and effectively.
Different Types of Straps and Their Capabilities
When selecting a strap for securing loads, you have options such as polypropylene, nylon, and Dyneema. Each type boasts different capabilities:
- Polypropylene: This is a cost-effective choice, suitable for lighter loads. It is resistant to moisture, chemicals, and rotting, yet it has a lower break strength compared to other materials. Type WLL Breaking Strength Polypropylene Strap Moderate Lower
- Nylon: Known for its elasticity, nylon can absorb shocks well. It’s a heavy-duty material, offering a higher WLL and breaking strength. However, it’s less resistant to environmental damage like acids and sunlight. Type WLL Breaking Strength Nylon Strap High Higher
- Dyneema: Often touted as the strongest fiber, Dyneema straps possess an exceptional strength-to-weight ratio, providing the highest WLL and break strength with less stretch than nylon. Type WLL Breaking Strength Dyneema Strap Very High Highest
Each strap typically includes fittings which also contribute to overall strength and functionality. The construction and quality of these fittings – whether hooks, buckles, or ratchets – must be compatible with both the WLL and breaking strength of the webbing they are used with.
Material Properties and Their Impact on WLL and Strength
The breaking strength and WLL of strapping material are not only determined by the material itself but also by the weave of the webbing. A tighter and more complex weave will generally increase strength. Here’s how materials stack up:
- Polypropylene is often used for light-duty applications; it’s durable but not ideal for heavy loads.
- Nylon, with its excellent recovery properties and strength, can handle higher WLLs, making it suited for more demanding applications.
- Dyneema outperforms others with its incredible tensile strength and minimal stretch, translating to the highest WLLs ideal for the most critical heavy lifting tasks.
Remember that regular inspection and understanding the specific properties of your strap material and construction help maintain safety standards and extend the life of your equipment.
Regulatory Standards and Compliance
In the context of load handling and equipment safety, understanding regulatory standards and compliance is essential for ensuring safety and adhering to legal requirements.
Manufacturers of lifting and rigging equipment must adhere to specific standards which define the rated capacity of their products. The rated capacity, which includes Working Load Limit (WLL) and Breaking Strength, must be clearly marked on the equipment. For the shipping industry, this is critical as it ensures the safety of cargo during transport. For example:
- OSHA (Occupational Safety and Health Administration) in the United States sets guidelines for safe working conditions, which includes the use of equipment within its WLL.
- ASME (American Society of Mechanical Engineers) provides standards for the design, testing, and inspection of hoisting and rigging equipment.
If you are interested in the regulations in this area, you can check it on its official website.
Choosing the Correct Equipment for Different Applications
When securing cargo or performing industrial lifts, it’s crucial to select the right equipment based on the Working Load Limit (WLL) and Breaking Strength (BS) to ensure safety and compliance.
Cargo Securing and Transportation
In the realm of cargo securing and transportation, it’s essential to choose the correct securing device for your vehicle. For instance:
- Ratchet Straps: Ideal for heavy-duty applications due to their robustness. They typically offer the ease of tightening and releasing tension with a ratchet mechanism. Strap Type Ideal Use Case Nylon Stretchable, for lighter loads Polyester Minimal stretch, for heavier loads
- Winch Straps: These are often used with a winch permanently mounted to your vehicle, which is beneficial for flatbed trucks and trailers. Strap Length Vehicle Compatibility 20-30 ft Small to Medium Trucks 30-50 ft Large Trucks and Trailers
The securing equipment should have a WLL that accommodates the weight and nature of the cargo, while the BS, as we talked before, should be at least three times the WLL, providing a sufficient safety margin.
Industrial Lifting and Rigging
For industrial lifting and rigging, the lifting device you select must match the task:
- Chains: These are durable and suited for heavy loads with sharp edges that might abrade or cut softer straps. Chain Grade Load Range Grade 80 Up to 7,000 lbs Grade 100 Up to 17,900 lbs
- Lifting Straps: Fabricated from fibers like nylon or polyester, these are better for delicate loads that can be damaged by chains.
The equipment’s WLL should be carefully matched to the load’s weight, and the BS should be a multiple of that WLL (commonly a factor of 5 or 6), ensuring a safe lifting operation. Choose a lifting device with comprehensive labeling indicating both WLL and BS for optimal safety.
Maintenance and Regular Inspection
The integrity of your rigging and lifting equipment is reliant on consistent maintenance and regular inspection. Keep these points in mind:
- Visual Inspections: Before each use, visually inspect your equipment for any signs of wear, damage, or fatigue.
- Scheduled Inspections: Adhere to the manufacturer’s guidelines for detailed, periodic inspections.
- Documentation: Keep a log of all inspections, maintenance, and repairs to track the equipment’s condition and history.
By doing so, you not only extend the lifespan of your equipment but also ensure the safety of everyone involved. Remember, compromised equipment can lead to dangerous situations, so never skip your inspections.