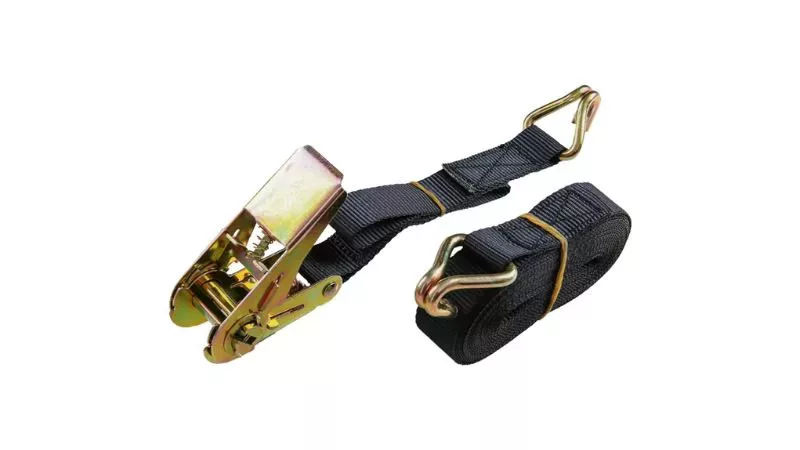
Ratchet straps are one of the most widely used tools for securing cargo, whether you’re a professional trucker hauling a flatbed trailer or just an occasional user tying down items in your pickup truck. But have you ever wondered exactly how much weight these handy tie-downs can safely handle? The key is understanding the working load limit.
However, the work load limit always be confused with breaking strength. This article will explain to you what is the working load limit, what is the breaking strength, the differences between them and the working limits of different ratchet straps.
What is the Safe Working Load Limit
The Safe Working Load (SWL), also known as the Working Load Limit (WLL), is the maximum load that a ratchet strap can safely lift, lower, or suspend without fear of breaking or failing.
Each strap has a working load limit tag, which is a label typically stitched into the webbing of the ratchet strap. It visibly displays the load rating the strap is designed for, usually expressed in pounds (lbs) or kilograms (kg).
What is the Breaking Strength
Breaking Strength represents the point at which your ratchet straps will fail under a load. It’s a measure of the tensile strength and the maximum load the strap can bear before breaking.
The WLL is typically calculated as one-third (1/3) or one-fourth(1/4) of the Breaking Strength of the strap’s weakest component, depending on the manufacturer and industry standards.
What is the Elongation of a Ratchet Strap?
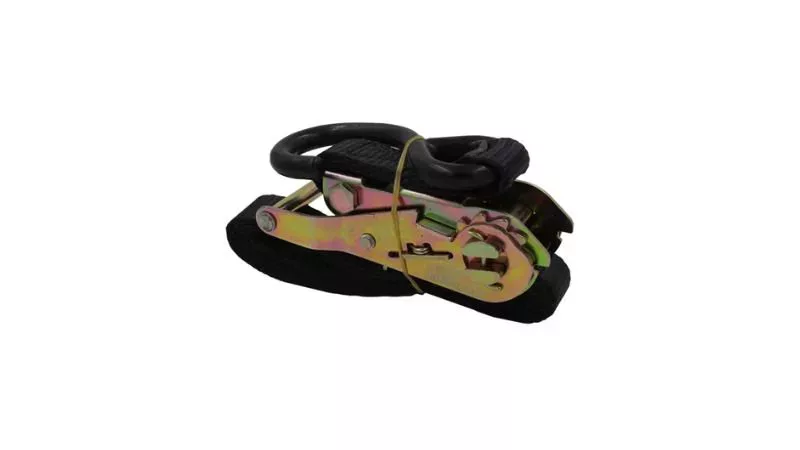
The elongation of a ratchet strap refers to the maximum amount the strap can stretch when fully tightened.
By law, the maximum elongation a ratchet strap is allowed to have is 7% of its total length. Most straps will have an average elongation of around 4%
How is the Load Capacity of a Ratchet Strap Determined?
The load capacity of a ratchet strap is largely determined by its width, the webbing material, and the hardware it uses.
Here are the details that determine a ratchet strap’s Working Load Limit:
- Strap width: Common widths range from 1″ for light-duty applications up to 4″ for the heaviest loads. A wider strap can safely handle more weight.
- Webbing material: Ratchet straps are typically made from durable polyester webbing. Polyester provides high strength and low stretch to keep loads secure.
- Hardware components: The WLL is determined by the lowest-rated component in the assembly, which could be the webbing itself, the ratchet, or the end fittings like flat hooks, wire hooks, grab hooks, chain extensions, snap hooks, D-rings, E-track, and L-track fittings.
What are the Weight Limits for Different Types of Ratchet Straps?
There are four main types of ratchet straps, each designed for different load capacities. The specific load limit also depends on the hardware used. The following are standard load ratings for reference.
- 1 inch Ratchet Straps
- Size: 12/16 feet of tie down webbing
- Rated for 500 lbs to 1,100 lbs WLL
- Used for lightweight applications like moving vans, pickup trucks, trailers, or lightweight cargo securement.
- 2 inch Ratchet Straps
- Size: 12/16 tie down webbing
- Rated for 915 lbs to 3,335 lbs WLL
- The most common size, used for heavier everyday tasks like securing motorcycles, ATVs
- Can have a WLL up to 5,000 lbs with a 15,000 lb break strength rating
- 3 inch Ratchet Straps
- Rated for 5,000 lb to 5,670 lb WLL
- Heavy and large, designed for flatbeds and heavy duty cargo.
- Not suitable for pickup trucks, move vans, and most household applications
- 4 inch Ratchet Straps
- Size:27/30 feet of tie down webbing
- Rated for 5,400 lb to 5,670 lb WLL
- Heaviest duty, used to secure the largest cargo on flatbeds and tractor-trailers
How Many Ratchet Tie-Down Straps are Needed to Secure Cargo?
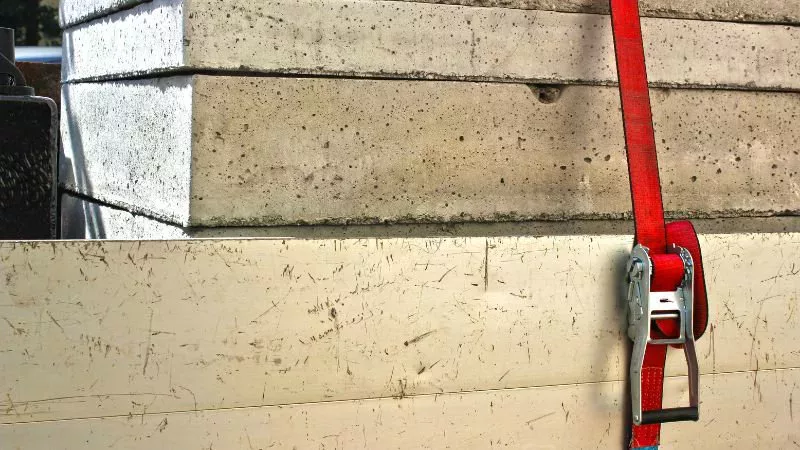
If the cargo is less than 5 feet long and weighs less than 1,100 lbs, use at least 1 tie-down strap.
If the cargo is less than 5 feet long but weighs more than 1,100 lbs or is between 5-10 feet long regardless of weight, use at least 2 tie-down straps.
For cargo longer than 10 feet, use 2 tie-down straps for the first 10 feet of length, plus 1 additional strap for every 10 feet after that. If the extra length is less than 10 feet, still add 1 more strap.
As a rule of thumb, if the cargo weighs over 10,000 lbs, use a minimum of 4 tie-down straps, with more straps being better to distribute the forces.
In most cases, to ensure heavy loads you need at least four tie-down straps, each attached at a different point. Commonly, four to six straps should be used.
The aggregate working load limit of all the straps used must be at least 50% of the total cargo weight. Each strap’s working load limit counts fully if both ends attach to the vehicle. If one end attaches to the cargo, only 50% of that strap’s limit counts.
How Does the Tie-down Angle Affect the Working Load Limit?
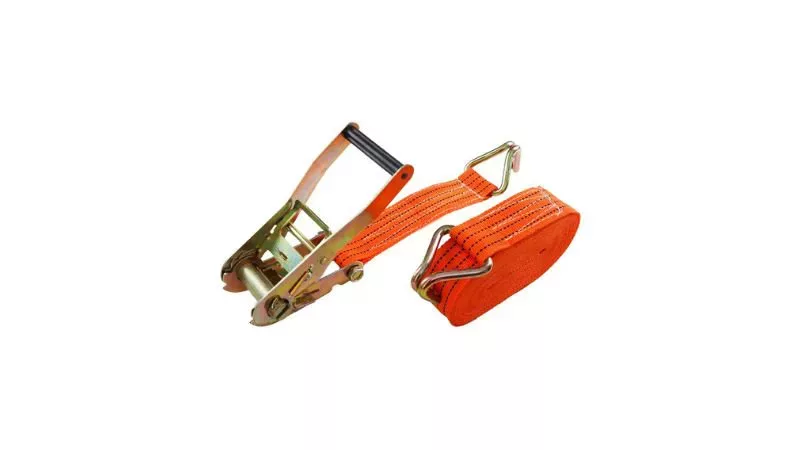
Tie-down straps are most effective when they are vertical (90° angle) and tightly tensioned. The more a strap is angled away from vertical, the less clamping force it applies to the load.
The tie-down angle effect reduces the strap’s effectiveness at lower angles:
- 90° angle: 100% effectiveness
- 60° angle: 85% effectiveness
- 45° angle: 70% effectiveness
- 30° angle: 50% effectiveness
- 15° angle: 25% effectiveness
For example, if a strap is tied at a 45° angle instead of 90°, the downward force is only around 70% of the strap’s maximum rating. So, a strap with a 5000 daN lashing capacity would only exert 3500 daN of force at a 45° angle.
To compensate for lower angles, more straps are needed to provide the same total clamping force. One strap at 90° is equivalent to four straps at 15°.
As a general rule, the angle of an indirect tie-down strap should always be at least 30° to maintain adequate effectiveness.
The actual securing effect of a tie-down strap reaches its maximum at a lashing angle of approximately 65° to 70°. Only at an angle of around 88° do small angle changes significantly reduce the securing effect.
Frequently Asked Questions
How many types of tie down straps?
Commonly, there are five different types: Ratchet Straps, Cam Buckle Straps, E-Track Straps, Winch Straps, and Lashing Straps.
What are the factors that affect the effectiveness of a ratchet strap?
The tie-down angle is a major factor, proper use and loading of the straps is also critical. Avoiding twists, knots, rubbing, overloading, and uneven winding helps ensure the straps can safely and effectively restrain the cargo at their rated capacity.